Since the beginning of the ongoing global public health crisis, we have done
our best to help our customers cope with this unprecedented situation. One of the challenges we have faced is how to continue offering them the same level of technical assistance and support they are used to, now that we cannot physically send our personnel to their factories.
We have tried to solve that problem the best way we know: through innovation. For years, we had been experimenting with remote access features. In fact, many of our newest
assembly lines already include
advanced networking functions, and can be linked to our
exclusive smartphone app to provide production statistics and other useful information in real time, as shown towards the end of this video:
But what about the hardware? How do you install an entire production line made up of several fully automated machines — all of them packed with sophisticated components that require careful calibration — when you cannot even take a plane? Enter our remote assistance paradigm.
For the last couple of months, we have been providing our customers free of charge with a small
wearable camera that is shipped together with our machines. The personnel on site can wear it during the installation or attach it to the machine, so that our engineers in Taiwan can get a clear picture of the situation and guide them accordingly.
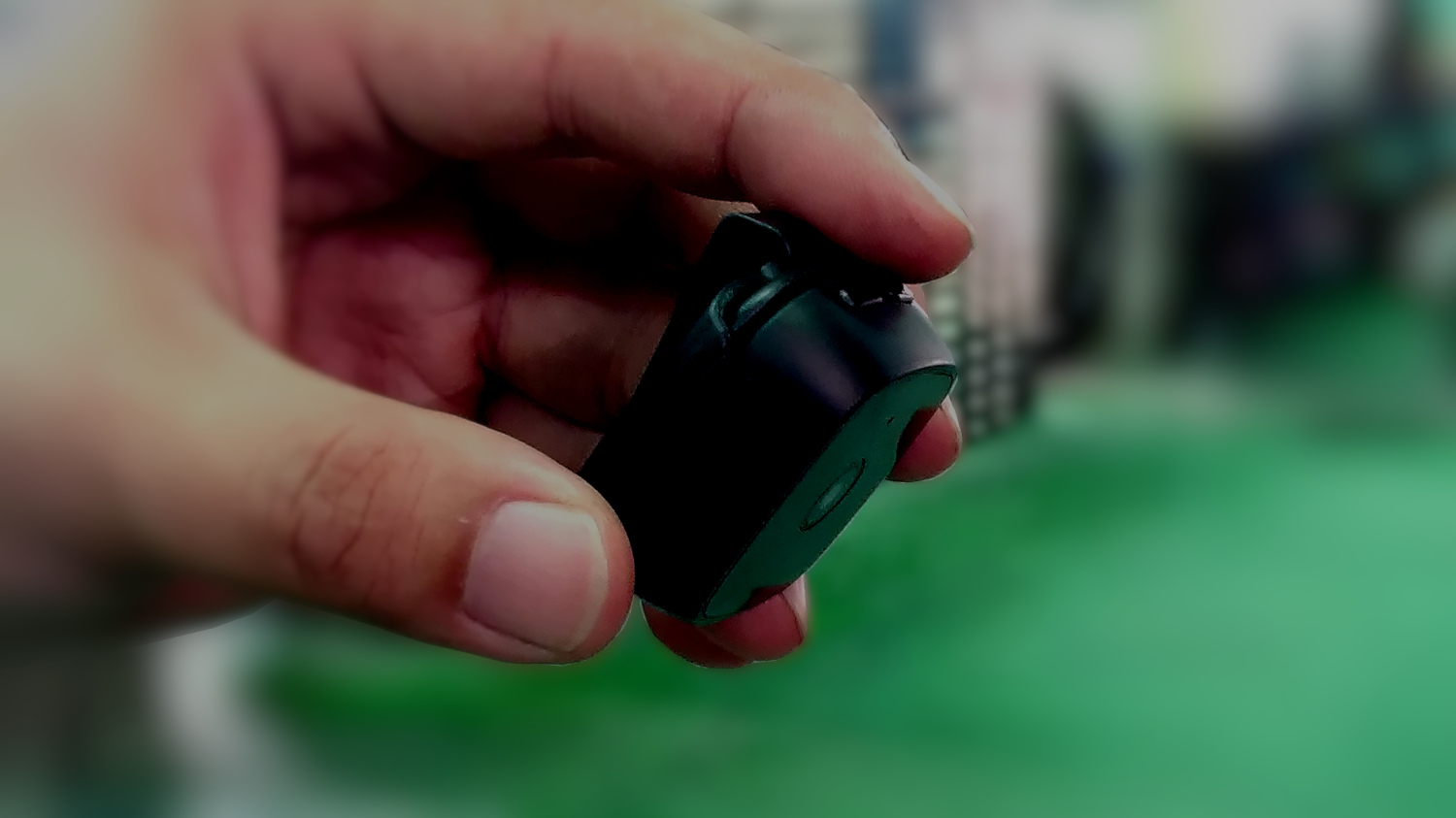
In some cases, we have also arranged for our customers to
virtually inspect their machines in our factory before shipment.
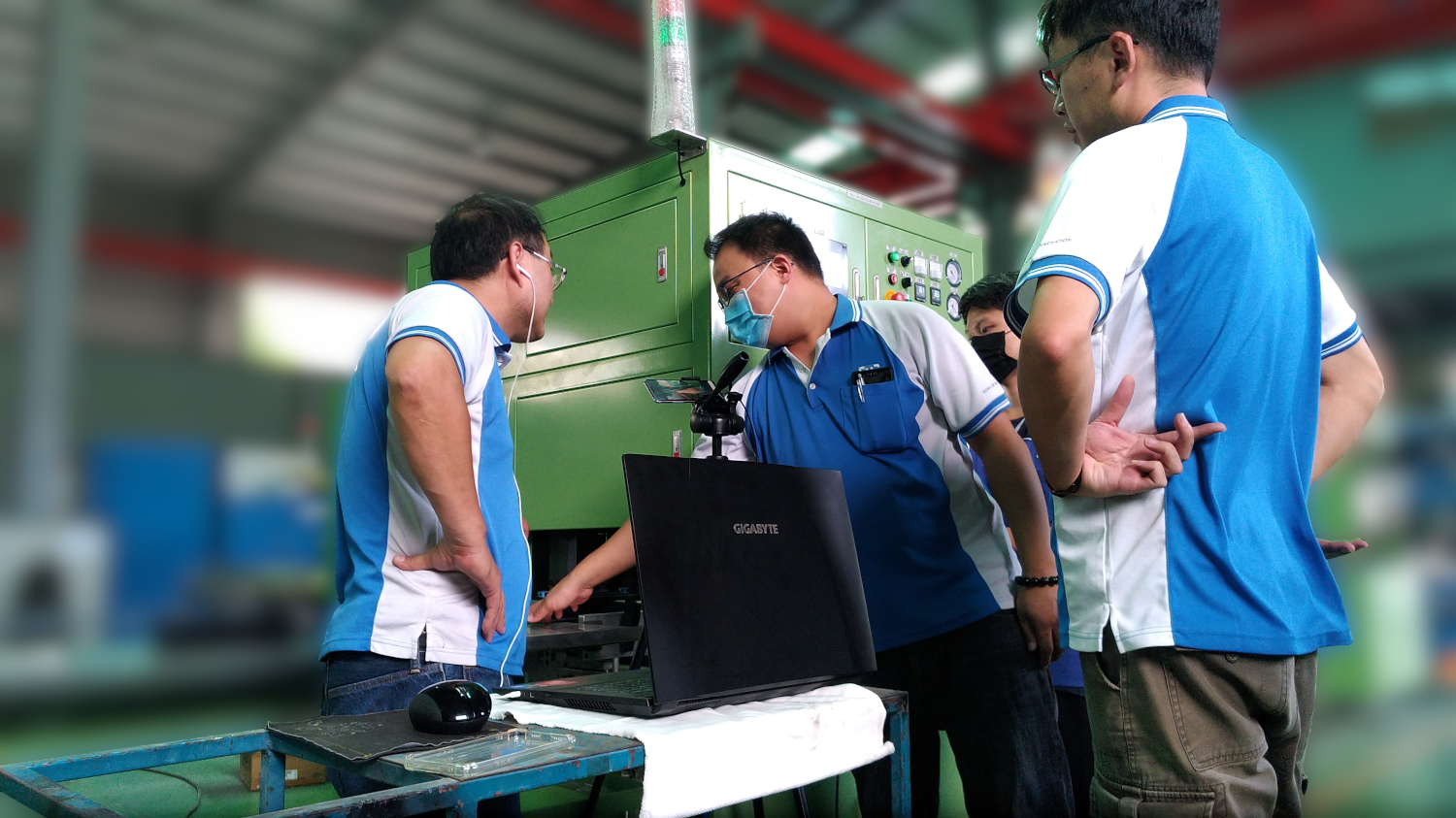
We have also revamped our machine instructions and installation manuals to adapt to the current situation. In some cases, we shot
hours of HD video detailing the most common installation, operation and maintenance procedures.
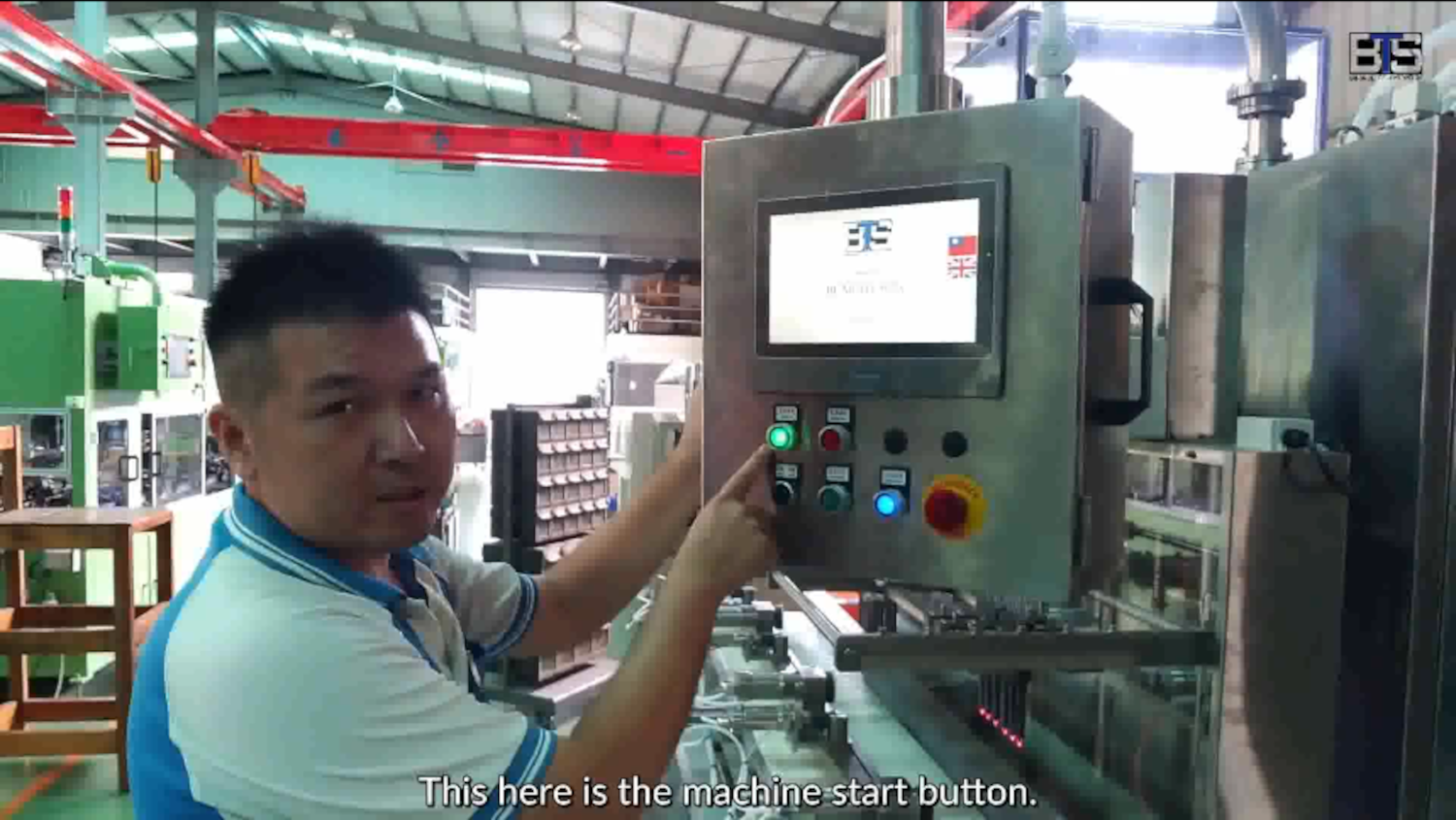
As much as we love to meet with our customers and partners in person, we understand that we have to be creative to help them stay successful through the pandemic and get ready for the recovery. More than ever, we want them — and you — to know
you can count on us.